As we return to the office, there is a growing reliance on devices to tell us how safe and secure the environment is for our return. And in specific application areas, such as Healthcare and Manufacturing, IoT data is critical for decision-making. In some sectors such as Health and Wellness, IoT devices collect personally identifiable information (PII). IoT technology is so critical to our current infrastructures that the physical wellbeing of both individuals and organisations can be at risk.
Trust & Data
IoT are also vulnerable to breaches if not properly secured. And with a significant increase in cybersecurity events over the last year, the reliance on data from IoT is driving the need for better data integrity. Security features such as data integrity and device authentication can be accomplished through the use of digital certificates and these features need to be designed as part of the device prior to manufacturing. Because if you cannot trust either the IoT devices and their data, there is no point in collecting, running analytics, and executing decisions based on the information collected.
We discuss the role of embedding digital certificates into the IoT device at manufacture to enable better security and ongoing management of the device.
Securing IoT Data from the Edge
So much of what is happening on networks in terms of real-time data collection happens at the Edge. But because of the vast array of IoT devices connecting at the Edge, there has not been a way of baking trust into the manufacture of the devices. With a push to get the devices to market, many manufacturers historically have bypassed efforts on security. Devices have been added on the network at different times from different sources.
There is a need to verify the IoT devices and secure them, making sure to have an audit trail on what you are connecting to and communicating with.
So from a product design perspective, this leads us to several questions:
- How do we ensure the integrity of data from devices if we cannot authenticate them?
- How do we ensure that the operational systems being automated are controlled as intended?
- How do we authenticate the device on the network making the data request?
Using a Public Key Infrastructure (PKI) approach maintains assurance, integrity and confidentiality of data streams. PKI has become an important way to secure IoT device applications, and this needs to be built into the design of the device. Device authentication is also an important component, in addition to securing data streams. With good design and a PKI management that is up to the task you should be able to proceed with confidence in the data created at the Edge.
Johnson Controls/DigiCert have designed a new way of managing PKI certification for IoT devices through their partnership and integration of the DigiCert ONE™ PKI management platform and the Johnson Controls OpenBlue IoT device platform. Based on an advanced, container-based design, DigiCert ONE allows organisations to implement robust PKI deployment and management in any environment, roll out new services and manage users and devices across your organisation at any scale no matter the stage of their lifecycle. This creates an operational synergy within the Operational Technology (OT) and IoT spaces to ensure that hardware, software and communication remains trusted throughout the lifecycle.

Rationale on the Role of Certification in IoT Management
Digital certificates ensure the integrity of data and device communications through encryption and authentication, ensuring that transmitted data are genuine and have not been altered or tampered with. With government regulations worldwide mandating secure transit (and storage) of PII data, PKI can help ensure compliance with the regulations by securing the communication channel between the device and the gateway.
Connected IoT devices interact with each other through machine to machine (M2M) communication. Each of these billions of interactions will require authentication of device credentials for the endpoints to prove the device’s digital identity. In such scenarios, an identity management approach based on passwords or passcodes is not practical, and PKI digital certificates are by far the best option for IoT credential management today.
Creating lifecycle management for connected devices, including revocation of expired certificates, is another example where PKI can help to secure IoT devices. Having a robust management platform that enables device management, revocation and renewal of certificates is a critical component of a successful PKI. IoT devices will also need regular patches and upgrades to their firmware, with code signing being critical to ensure the integrity of the downloaded firmware – another example of the close linkage between the IoT world and the PKI world.
Summary
PKI certification benefits both people and processes. PKI enables identity assurance while digital certificates validate the identity of the connected device. Use of PKI for IoT is a necessary trend for sense of trust in the network and for quality control of device management.
Identifying the IoT device is critical in managing its lifespan and recognizing its legitimacy in the network. Building in the ability for PKI at the device’s manufacture is critical to enable the device for its lifetime. By recognizing a device, information on it can be maintained in an inventory and its lifecycle and replacement can be better managed. Once a certificate has been distributed and certified, having the control of PKI systems creates life-cycle management.
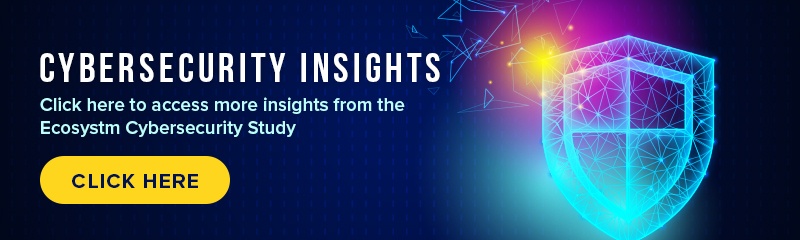
In this Insight, our guest author Anupam Verma talks about how the Global Capability Centres (GCCs) in India are poised to become Global Transformation Centres. “In the post-COVID world, industry boundaries are blurring, and business models are being transformed for the digital age. While traditional functions of GCCs will continue to be providing efficiencies, GCCs will be ‘Digital Transformation Centres’ for global businesses.”
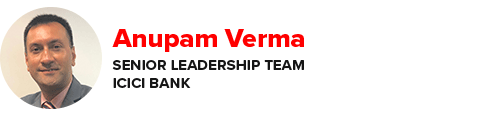
India has a lot to offer to the world of technology and transformation. Attracted by the talent pool, enabling policies, digital infrastructure, and competitive cost structure, MNCs have long embraced India as a preferred destination for Global Capability Centres (GCCs). It has been reported that India has more than 1,700 GCCs with an estimated global market share of over 50%.
GCCs employ around 1 million Indian professionals and has an immense impact on the economy, contributing an estimated USD 30 billion. US MNCs have the largest presence in the market and the dominating industries are BSFI, Engineering & Manufacturing, Tech & Consulting.
GCC capabilities have always been evolving
The journey began with MNCs setting up captives for cost optimisation & operational excellence. GCCs started handling operations (such as back-office and business support functions), IT support (such as app development and maintenance, remote IT infrastructure, and help desk) and customer service contact centres for the parent organisation.
In the second phase, MNCs started leveraging GCCs as centers of excellence (CoE). The focus then was product innovation, Engineering Design & R&D. BFSI and Professional Services firms started expanding the scope to cover research, underwriting, and consulting etc. Some global MNCs that have large GCCs in India are Apple, Microsoft, Google, Nissan, Ford, Qualcomm, Cisco, Wells Fargo, Bank of America, Barclays, Standard Chartered, and KPMG.
In the post-COVID world, industry boundaries are blurring, and business models are being transformed for the digital age. While traditional functions of GCCs will continue to be providing efficiencies, GCCs will be “Digital Transformation Centres” for global businesses.
The New Age GCC in the post-COVID world
On one hand, the pandemic broke through cultural barriers that had prevented remote operations and work. The world became remote everything! On the other hand, it accelerated digital adoption in organisations. Businesses are re-imagining customer experiences and fast-tracking digital transformation enabled by technology (Figure 1). High digital adoption and rising customer expectations will also be a big catalyst for change.
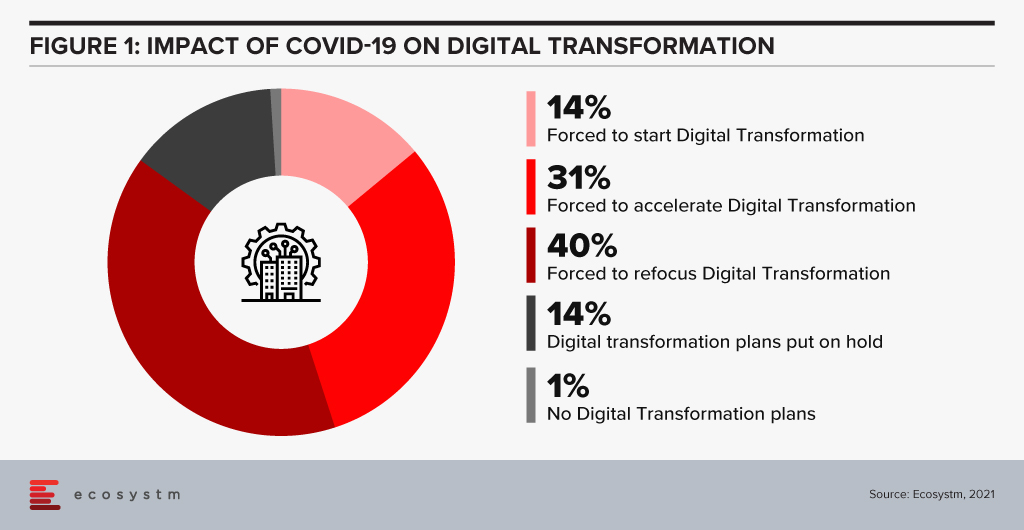
In last few years, India has seen a surge in talent pool in emerging technologies such as data analytics, experience design, AI/ML, robotic process automation, IoT, cloud, blockchain and cybersecurity. GCCs in India will leverage this talent pool and play a pivotal role in enabling digital transformation at a global scale. GCCs will have direct and significant impacts on global business performance and top line growth creating long-term stakeholder value – and not be only about cost optimisation.
GCCs in India will also play an important role in digitisation and automation of existing processes, risk management and fraud prevention using data analytics and managing new risks like cybersecurity.
More and more MNCs in traditional businesses will add GCCs in India over the next decade and the existing 1,700 plus GCCs will grow in scale and scope focussing on innovation. Shift of supply chains to India will also be supported by Engineering R & D Centres. GCCs passed the pandemic test with flying colours when an exceptionally large workforce transitioned to the Work from Home model. In a matter of weeks, the resilience, continuity, and efficiency of GCCs returned to pre-pandemic levels with a distributed and remote workforce.
A Final Take
Having said that, I believe the growth spurt in GCCs in India will come from new-age businesses. Consumer-facing platforms (eCommerce marketplaces, Healthtechs, Edtechs, and Fintechs) are creating digital native businesses. As of June 2021, there are more than 700 unicorns trying to solve different problems using technology and data. Currently, very few unicorns have GCCs in India (notable names being Uber, Grab, Gojek). However, this segment will be one of the biggest growth drivers.
Currently, only 10% of the GCCs in India are from Asia Pacific organisations. Some of the prominent names being Hitachi, Rakuten, Panasonic, Samsung, LG, and Foxconn. Asian MNCs have an opportunity to move fast and stay relevant. This segment is also expected to grow disproportionately.
New age GCCs in India have the potential to be the crown jewel for global MNCs. For India, this has a huge potential for job creation and development of Smart City ecosystems. In this decade, growth of GCCs will be one of the core pillars of India’s journey to a USD 5 trillion economy.
The views and opinions mentioned in the article are personal.
Anupam Verma is part of the Senior Leadership team at ICICI Bank and his responsibilities have included leading the Bank’s strategy in South East Asia to play a significant role in capturing Investment, NRI remittance, and trade flows between SEA and India.
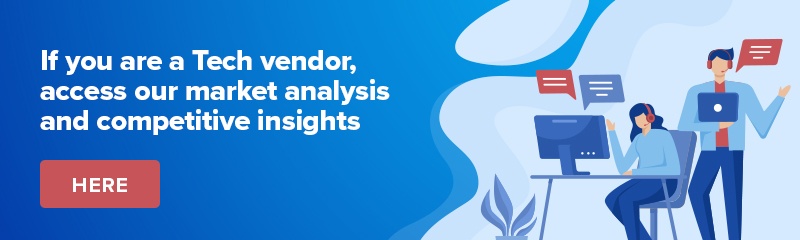
In 2020, much of the focus for organisations were on business continuity, and on empowering their employees to work remotely. Their primary focus in managing customer experience was on re-inventing their product and service delivery to their customers as regular modes were disrupted. As they emerge from the crisis, organisations will realise that it is not only their customer experience delivery models that have changed – but customer expectations have also evolved in the last few months. They are more open to digital interactions and in many cases the concept of brand loyalty has been diluted. This will change everything for organisations’ customer strategies. And digital technology will play a significant role as they continue to pivot to succeed in 2021 – across regions, industries and organisations.
Ecosystm Advisors Audrey William, Niloy Mukherjee and Tim Sheedy present the top 5 Ecosystm predictions for Customer Experience in 2021. This is a summary of the predictions – the full report (including the implications) is available to download for free on the Ecosystm platform.
The Top 5 Customer Experience Trends for 2021
- Customer Experience Will Go Truly Digital
COVID-19 made the few businesses that did not have an online presence acutely aware that they need one – yesterday! We have seen at least 4 years of digital growth squeezed into six months of 2020. And this is only the beginning. While in 2020, the focus was primarily on eCommerce and digital payments, there will now be a huge demand for new platforms to be able to interact digitally with the customer, not just to be able to sell something online.
Digital customer interactions with brands and products – through social media, online influencers, interactive AI-driven apps, online marketplaces and the like will accelerate dramatically in 2021. The organisations that will be successful will be the ones that are able to interact with their customers and connect with them at multiple touchpoints across the customer journey. Companies unable to do that will struggle.
- Digital Engagement Will Expand Beyond the Traditional Customer-focused Industries
One of the biggest changes in 2020 has been the increase in digital engagement by industries that have not traditionally had a strong eye on CX. This trend is likely to accelerate and be further enhanced in 2021.
Healthcare has traditionally been focused on improving clinical outcomes – and patient experience has been a byproduct of that focus. Many remote care initiatives have the core objective of keeping patients out of the already over-crowded healthcare provider organisations. These initiatives will now have a strong CX element to them. The need to disseminate information to citizens has also heightened expectations on how people want their healthcare organisations and Public Health to interact with them. The public sector will dramatically increase digital interactions with citizens, having been forced to look at digital solutions during the pandemic.
Other industries that have not had a traditional focus on CX will not be far behind. The Primary & Resources industries are showing an interest in Digital CX almost for the first time. Most of these businesses are looking to transform how they manage their supply chains from mine/farm to the end customer. Energy and Utilities and Manufacturing industries will also begin to benefit from a customer focus – primarily looking at technology – including 3D printing – to customise their products and services for better CX and a larger share of the market.
- Brands that Establish a Trusted Relationship Can Start Having Fun Again
Building trust was at the core of most businesses’ CX strategies in 2020 as they attempted to provide certainty in a world generally devoid of it. But in the struggle to build a trusted experience and brand, most businesses lost the “fun”. In fact, for many businesses, fun was off the agenda entirely. Soft drink brands, travel providers, clothing retailers and many other brands typically known for their fun or cheeky experiences moved the needle to “trust” and dialed it up to 11. But with a number of vaccines on the horizon, many CX professionals will look to return to pre-pandemic experiences, that look to delight and sometimes even surprise customers.
However, many companies will get this wrong. Customers will not be looking for just fun or just great experiences. Trust still needs to be at the core of the experience. Customers will not return to pre-pandemic thinking – not immediately anyway. You can create a fun experience only if you have earned their trust first. And trust is earned by not only providing easy and effective experiences, but by being authentic.
- Customer Data Platforms Will See Increased Adoption
Enterprises continue to struggle to have a single view of the customer. There is an immense interest in making better sense of data across every touchpoint – from mobile apps, websites, social media, in-store interactions and the calls to the contact centre – to be able to create deeper customer profiles. CRM systems have been the traditional repositories of customer data, helping build a sales pipeline, and providing Marketing teams with the information they need for lead generation and marketing campaigns. However, CRM systems have an incomplete view of the customer journey. They often collect and store the same data from limited touchpoints – getting richer insights and targeted action recommendations from the same datasets is not possible in today’s world. And organisations struggled to pivot their customer strategies during COVID-19. Data residing in silos was an obstacle to driving better customer experience.
We are living in an age where customer journeys and preferences are becoming complex to decipher. An API-based CDP can ingest data from any channel of interaction across multiple journeys and create unique and detailed customer profiles. A complete overhaul of how data can be segregated based on a more accurate and targeted profile of the customer from multiple sources will be the way forward in order to drive a more proactive CX engagement.
- Voice of the Customer Programs Will be Transformed
Designing surveys and Voice of Customer programs can be time-consuming and many organisations that have a routine of running these surveys use a fixed pattern for the data they collect and analyse. However, some organisations understand that just analysing results from a survey or CSAT score does not say much about what customers’ next plan of action will be. While it may give an idea of whether particular interactions were satisfactory, it gives no indication of whether they are likely to move to another brand; if they needed more assistance; if there was an opportunity to upsell or cross sell; or even what new products and services need to be introduced. Some customers will just tick the box as a way of closing off a feedback form or survey. Leading organisations realise that this may not be a good enough indication of a brand’s health.
Organisations will look beyond CSAT to other parameters and attributes. It is the time to pay greater attention to the Voice of the Customer – and old methods alone will not suffice. They want a 360-degree view of their customers’ opinions.
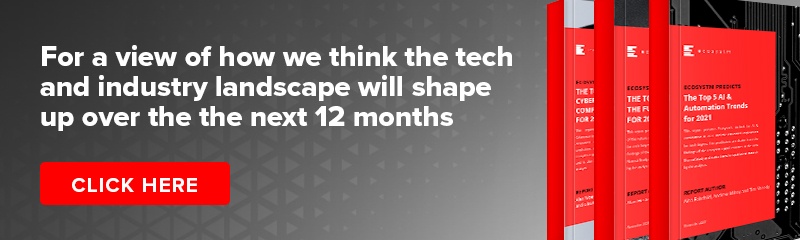
As the search for a COVID-19 vaccine intensifies, there is a global focus on the Life Sciences industry. The industry has been hit hard this year – having to deliver overtime through a disrupted supply chain, unexpected demand spikes, and reduction of revenues from their regular streams. Life sciences organisations are already challenged by the breadth of their focus – across R&D and clinical discovery; Manufacturing & Distribution; and Sales & Marketing. Increasingly, many pharmaceutical and medtech organisations choose to outsource some of these functions, which brings to fore the need for a robust compliance framework. In the Ecosystm Digital Priorities in the New Normal Study, two-thirds of life sciences organisations mention that they have either been forced to start, accelerate or refocus their Digital Transformation initiatives – the remaining one-third have put their Digital Transformation on hold. The industry is clearly at an inflection point.
Challenges of the Life Sciences Industry
Continued Focus on R&D. Life sciences companies operate in an extremely competitive global market where they have to work on new products against a backdrop of competition from generics and a global concern over rising healthcare expenditure. Apart from regulatory challenges, they also face immense competition from local manufacturers as they enter each new market.
Re-thinking their Distribution Strategy. Sales and distribution for many pharma and medtech organisations have been traditional – using agents, distributors, clinicians, and healthcare providers. But now they need to change their go-to-market strategies, target patients and consumers directly and package their product offerings into value-added services. This will require them to incorporate customer experience enhancers in their R&D, going beyond drug discovery and product innovation.
Tracking Global Regulations. Governments across the world are trying to manage their healthcare budgets. They are also more focused on chronic disease management. The focus has shifted to value-based medicine in general, but pharma and medtech products are being increasingly held accountable by health outcomes. Governments are increasingly implementing drug reforms around what clinicians can prescribe. Global Life Sciences organisations have to constantly monitor the regulations in the multiple countries where they operate and sell. They are also accountable for their entire supply chain, especially ensuring a high product quality and fraud prevention.
The global Ecosystm AI study reveals the top priorities for Life Sciences organisations, focused on adopting emerging technologies (Figure 1). They appear to be investing in emerging technology especially in their R&D and clinical discovery and Manufacturing functions.
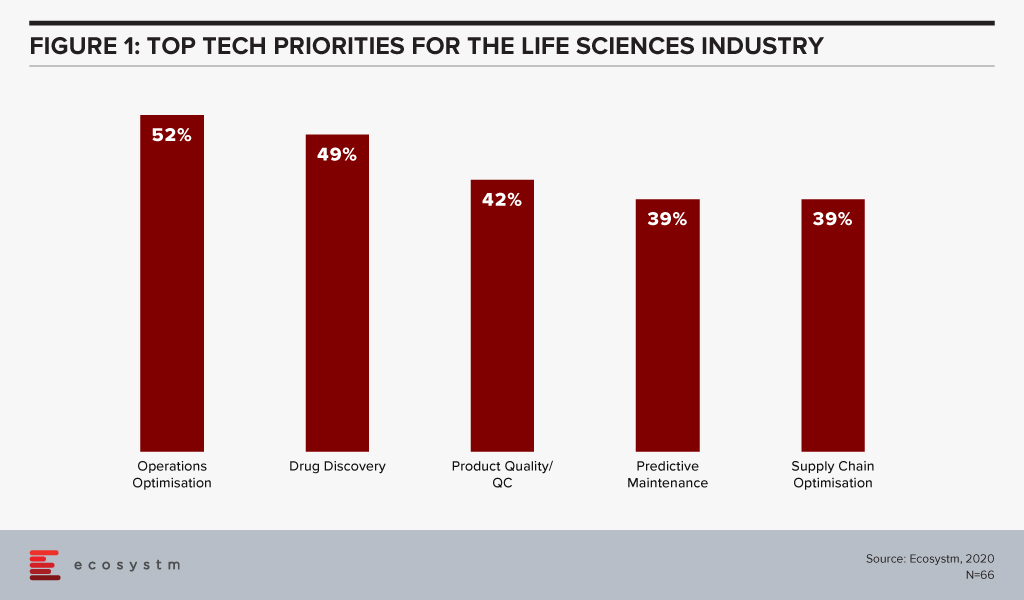
Technology as an Enabler of Life Sciences Transformation
Discovery and Development
With the evolution of technology, Life Sciences organisations are able to automate much of the mundane tasks around drug discovery and apply AI and machine learning to transform their drug discovery and development process. They are increasingly leveraging their ecosystem of smaller pharma and medtech companies, research laboratories, academic institutions, and technology providers to make the process more time and cost efficient.
Using an AI algorithm, the researchers at the Massachusetts Institute of Technology have discovered an antibiotic compound that can kill many species of antibiotic-resistant bacteria. MIT’s algorithm screens millions of chemical compounds and chooses the antibiotics which have the potential to eliminate bacteria resistant to existing drugs. Harvard’s Wyss Institute for Biologically Inspired Engineering is manufacturing 3D printed organ-on-a-chip to give insights on cell, tissue, and organ biology to help the pharma sector with drug development, disease modelling and finally in the development of personalised medicine.
Life Sciences are also engaging more with technology partners – whether emerging start-ups or established players. Pfizer and Saama are working together on AI clinical data mining. The companies are developing and deploying an AI-based analytical tool where Pfizer provides clinical data and domain knowledge to train models on the Saama Life Science Analytics Cloud (LSAC). Saama was identified as a partner at a hackathon. Sanofi and Google have established a new virtual Innovation Lab to develop scientific and commercial solutions, using multiple Google capabilities from cloud computing to AI.
Tech providers also keep evolving their capabilities in the Life Sciences industry for more efficient drug discovery and better treatment protocols. Microsoft’s Project Hanover uses machine learning to develop a personalised drug protocol to manage acute myeloid leukaemia. Similarly, Apple’s ResearchKit – an open-source framework is meant to help researchers and developers create iOS-based applications in the field of medical research.
Manufacturing and Logistics
The industry also faces the challenges faced by any Manufacturing organisation and has the need to deploy manufacturing analytics, and advanced supply chain technology for better process and optimisation and agility. There is also the need for complete visibility over their supply chain and inventory for traceability, safety, and fraud prevention. Emerging technologies such as Blockchain will become increasingly relevant for real-time track and trace capability.
The MediLedger Network was established as an open network to the entire pharma supply chain. The project brings a consortium of some of the world’s largest pharmaceutical companies, and logistics providers to improve drug supply chain management.
Since the data on the distributed ledger is encrypted, it creates a secure system without any vulnerabilities. This eliminates counterfeit products and ultimately ensures the quality of the pharma products and promotes increased patient safety. To foster security and improve the supply chain, the United States Food and Drug Administration (USFDA) successfully completed a pilot with a group including IBM, KPMG, Merck and Walmart to support U.S. Drug Supply Chain Security Act (DSCSA) to trace vaccines and prescription medicines throughout the country.
Diagnostics and Personalised Healthcare
As more devices (consumer and enterprise) and applications enter the market, people will take ownership and interest in their own health outcomes. This is seeing a continued growth in online communities and comparison sites (on physicians, hospitals, and pharmaceutical products). Increasingly, insurance providers will use data from wearable devices for a more personalised approach; promoting and rewarding good health practices.
Beyond the use of wearables and health and wellness apps, we will also see an exponential increase of home-based healthcare products and services – whether for primary care and chronic disease management, or long-term and palliative care. As patients become more engaged with their care, the life sciences industry is beginning to serve them through personalised approach, medicines, right diagnosis and through advanced medical devices and products.
An online tool developed by the University of Virginia Health Systems helps identify patients that have a high risk of getting a stroke and helps them reduce that risk. This tool calculates the patient’s probability of suffering a stroke by measuring the severity of their metabolic syndrome – taking into account a number of conditions that include high blood pressure, abnormal cholesterol levels and excess body fat. Life Sciences organisations are increasingly having to invest in customer-focused solutions such as these.
Wearables with special smart software to monitor health parameters, gauge drug compatibility and monitor complications are being implemented by Life Sciences organisations. The US FDA approved a pill called Abilify MyCite fitted with a tiny ingestible sensor that communicates with a patch worn by the patient to transmit data on a smartphone. Medtech companies continue to develop FDA approved health devices that can monitor chronic conditions. Smart continuous glucose monitoring (CGM) and insulin pens send blood glucose level data to smartphone applications allowing the wearer to easily check their information and detect trends.
Technologies such as AR/VR are also enabling Life Sciences companies with their diagnostics. Regeneron Pharmaceuticals has created an AR/VR app called “In My Eyes” to better diagnose vision impairment in patients.
What is interesting about these personalised products is that not only do they improve clinical outcomes, they also give Life Sciences companies access to rich data that can be used for further product development and improvement.
The Life Sciences industry will continue to operate in an unpredictable and competitive market. This is evident by the several mergers and acquisitions that we witness in the industry. As they continue to use cutting-edge technology for their R&D practices, they will leverage technology to transform other functions as well.
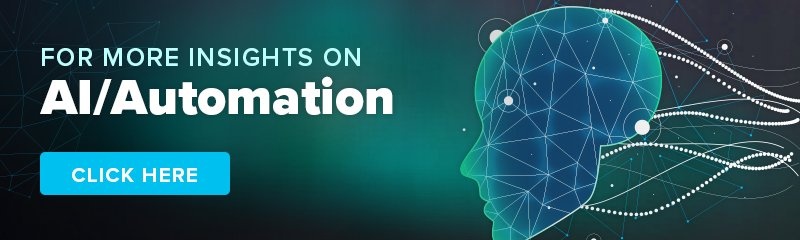
We continue to receive responses from the tech buyer community on the impact of COVID-19 on Digital Transformation initiatives, and the early business and technology measures that were implemented to combat the crisis. As the months go by, it is becoming apparent that organisations have implemented the early measures and are now looking ahead to their journey to recovery.
IT Teams realised that even if they had the right technology solutions, they were unprepared for the scale or capacity to extend these technology offerings to handle the sudden and enormous changes required to manage the crisis. Their cloud business applications, cybersecurity and collaboration solutions were simply not sufficient to meet the needs of the remote workforce. As organisations become more conscious of business continuity planning (BCP) for future eventualities, they will boost their technology capabilities, over the next 12 months.
Another area the study aims to explore is how optimistic is the business outlook, when it comes to expecting a return to normalcy. Only 3% of organisations are expecting a New Normal that is very different from where things were at the beginning of the year. About a third of organisations are expecting a return to normalcy by the end of the year, while the majority expect to recover by the middle of 2021. Also, some industries are more optimistic of a recovery than others. As an example, 35% of healthcare organisations expect a return to normalcy by the end of the year. This is a positive indicator, given that the industry has been in the forefront of the crisis, for nearly 6 months now.
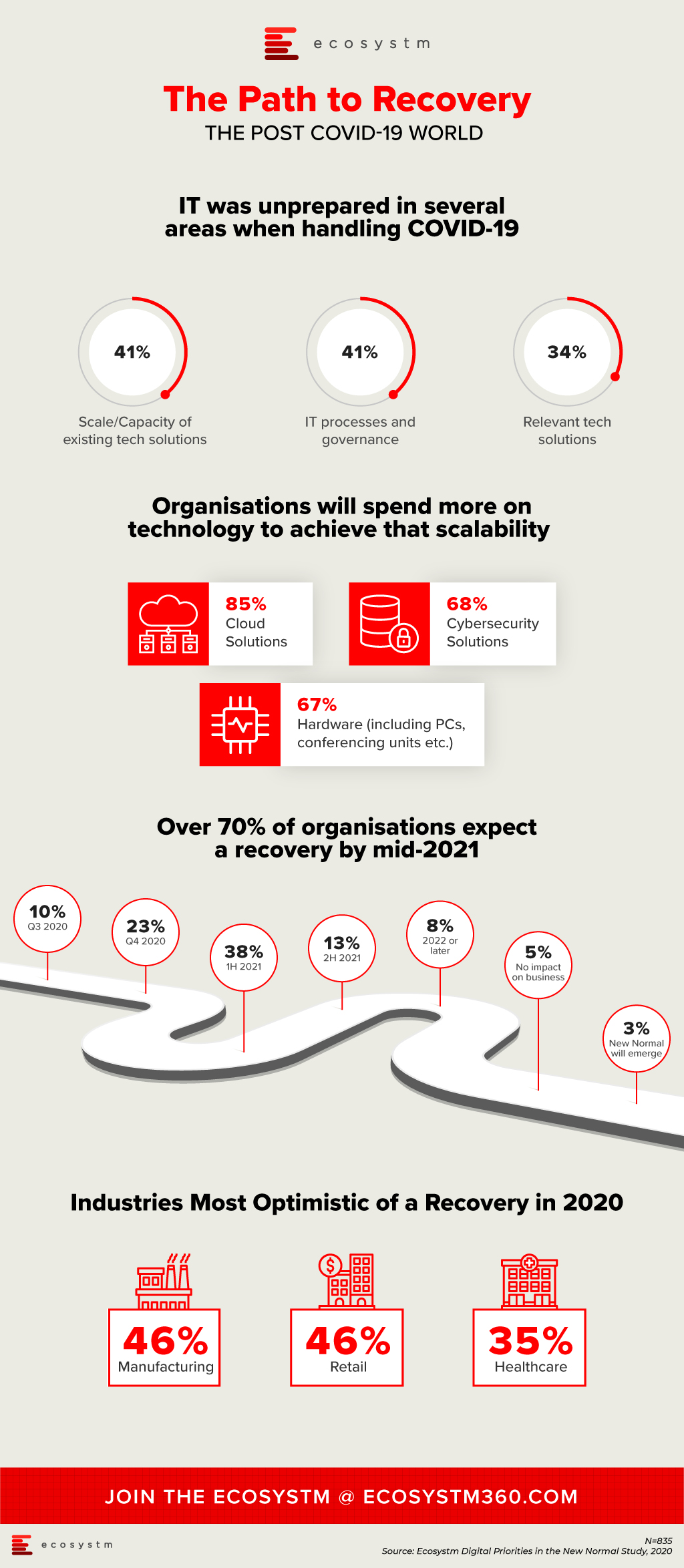
More insights on the impact of the COVID-19 pandemic and technology areas that will see continued investments, as organisations get into the recovery phase, can be found in the Digital Priorities in the New Normal Study.
In recent times, there appears to be a shift in motive for cyber-attacks – along with common data theft, there is a proliferation of attacks aimed at the business interruption and physical incapacitation of business operations. We have witnessed an alarming increase in high-profile attacks on manufacturing businesses and critical infrastructure providers, globally.
This appears to be a global phenomenon. Honda manufacturing plants went offline in June after a cyber-attack compromised some of the Japanese automaker’s facilities. The same pattern emerged in a separate attack at the same time targeting Edesur S.A., a company belonging to the Enel Group that confirmed its internal IT network was disrupted due to a ransomware attack, which was caught by antivirus software before the malware could infect. Both companies had machines with Internet-accessible remote desktop servers, which is a favorite infection method among attackers nowadays. One of Australia’s largest brewers, Lion also faced a ransomware outbreak, last month. In Israel, it was reported that a cyber-attack very nearly poisoned the water supply with the attackers attempting to overload the water system with chlorine, and in recent days, a fire and explosion at an Iranian nuclear plant is suspected of being caused by cyber-attack.
These attacks highlight the need for appropriate investments in cybersecurity by companies and municipalities that own or operate critical infrastructure, properties (including places of public congregation, retailers and others) that are rapidly deploying a suite of operational technologies, and businesses in the manufacturing sector.
Operational Technology (OT) is the backbone of modern industrial operations and is a network of multiple computing systems that perform operations including production line management, operations control and industrial monitoring. OT can further include specific computing systems like industrial control systems (ICS) which is a collection of control systems used to operate and/or automate industrial processes. There are several types of ICSs, the most common of which are Supervisory Control and Data Acquisition (SCADA) systems, and Distributed Control Systems (DCS). With such industrial systems and smart end-user products connected by a common network, several vulnerabilities may appear.
In OT security, the focus is much less on information, but more on the industrial process that technology controls. Hence, availability and integrity are often more important than confidentiality. Any organisation employing OT should employ continual risk-based assessments of their cybersecurity posture to prioritise and tailor recommended guidelines and solutions to fit specific security, business, and operational requirements.
Why is OT More Vulnerable?
OT systems are versatile and can be found in all kinds of industrial settings and infrastructures like smart buildings, oil and gas, energy generation/distribution, mining, wastewater treatment/distribution, manufacturing, food production, consumer devices and transport. In fact, almost every business in 2020 has an element of IoT within their operations.
A big issue with OT is that a lot of the technology in place is over 20 years old and therefore was not designed to provide the security capabilities required to face cyber threats in 2020. Legacy technology often requires legacy hardware and software to support it – much of which is the end of life and unsupported by the vendors (for example, consider SCADA systems still reliant on Windows NT or older Unix based systems, which have not been supported by their vendors for many years).
OT systems have also been damaged as unintended side effects of problems starting in corporate networks that took advantage of increasing connectivity, proving clearly that the standard PCs that now form part of a typical organisation’s IT environment are in turn used to manage OT systems and become a major vector for such cyber-attacks.
When it comes to OT, safety and reliability are the primary concerns as attackers aim to disrupt the critical services industry and their customers rely upon them. Given the increasing propensity of connecting OT systems with corporate networks for ease of management and the growing use of IoT systems, the likelihood of such systems being affected by vulnerabilities exploitable over the network is increasing exponentially.
For almost every business – not just critical infrastructure providers – most technologies we deploy include connectivity to the internet. Not knowing what systems and external access to these systems that your business is introducing in its everyday technology investment create significant risks to the broader business operations.
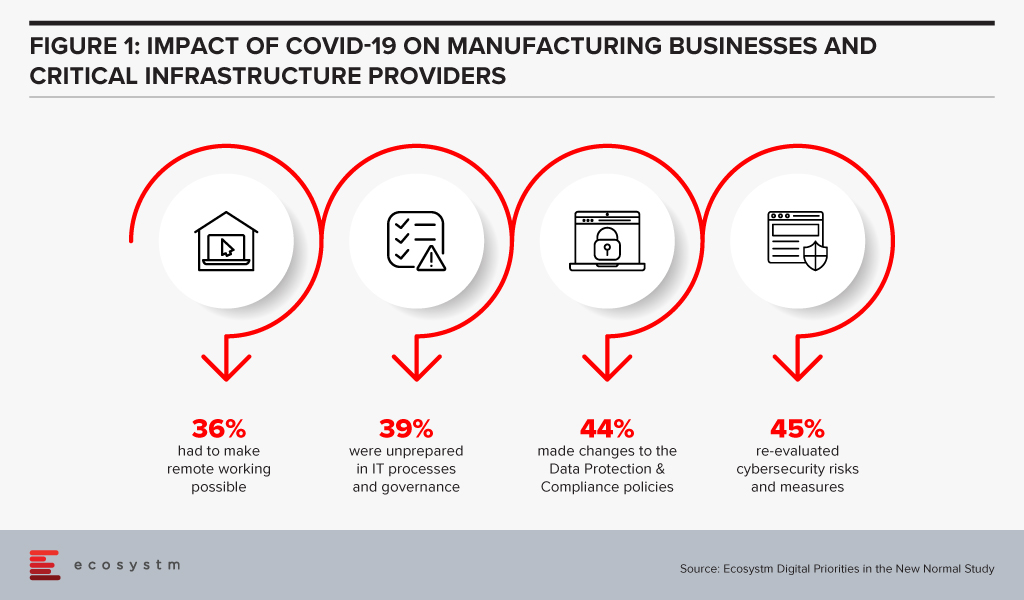
Manufacturing businesses and critical infrastructure providers realise that there is need to re-evaluate their cybersecurity measures, in the wake of the COVID-19 crisis, according to the findings of the Ecosystm’s ongoing “Digital Priorities in the New Normal” study (Figure 1).
But these measures may not be sufficient, as indicated by the slew of cyber-attacks on these organisations.
Why are these attacks successful?
There are several reasons why OT attacks are successful:
- Unauthorised access to internet-facing systems (e.g. deploying an IoT with the default username and password)
- Introduction of a compromised device (e.g. USB stick) to the environment that infects the network (often employee action)
- Exploitation of zero-day vulnerabilities in control devices and software
- Propagated malware infections within isolated computer networks (i.e. The attacker can place a receiving device to make contact over a channel that can propagate across the isolated network)
- SQL injection via exploitation of web application vulnerabilities
- Network scanning and probing
- Lateral movement (i.e. inadequate segmentation which results in attackers being able to move between systems, groups of systems, network zones and even geographical locations.)
How can they be prevented?
The mitigation cannot rely solely on the organisation building security around the deployment nor can it be a reactive approach to fixing vulnerabilities in production, as they are identified. It begins with the OT vendors building security within; however, as with most IT systems and applications, this will evolve over time. For example, there is an initiative in Australia – driven by the IoT Alliance Australia (IOTAA) – to introduce a ‘Trust Mark’ for IoT devices that pass a certification process for security and privacy in product development. This is targeted to launch in September 2020 but could take many years to gain real traction. Thus, for the foreseeable future, the best operational outcomes must be planned and managed by the consumers of the technologies.
Here are the best practices to reduce exploitable IoT weaknesses and attacks occurring in your business:
- Maintain an accurate inventory of Operational Systems and eliminate any exposure of these systems to external networks
- Establish clear roles and responsibilities for your organisation and your vendors, to ensure cybersecurity risk is being addressed and managed throughout the OT lifecycle
- Implement network segmentation and apply firewalls between critical networks and systems.
- Use secure remote access methods
- Establish Role-Based Access Controls (RBAC) and implement system logging
- Use only strong passwords, change default passwords, and consider other access controls (especially for any elevated privileges) such as multi-factor authentication, privileged access management solutions, etc.
- Establish threat intelligence feeds from your OT vendors and security vendors to ensure you remain abreast of new vulnerabilities, software/firmware patches and threats targeting systems you employ
- Develop and enforce policies on mobile devices, including strict device controls for any device connecting to OT systems or network zones
- Implement an employee cybersecurity training program
- Establish and maintain rigorous testing and patching program including vulnerability assessment and penetration testing
- Implement measures for detecting compromises and develop a cybersecurity incident response plan with a specific focus on responding to a disruptive attack on your OT environment
- Maintain an up-to-date Business Continuity Plan that can be deployed rapidly in response to a significant disruption
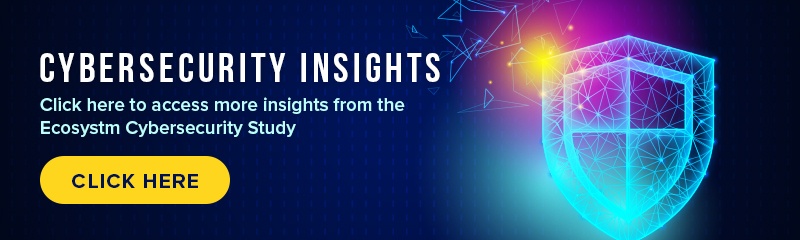
Manufacturing is estimated to account for a fifth of Singapore’s GDP and is one of its growth pillars. Singapore has been talking about re-inventing the Manufacturing industry since 2017, when the Industry 4.0 initiatives to enable digitalisation and process automation of processes and to ensure global competitiveness were first launched. As part of the long-term strategy, the Government had spoken about investment into research and development (R&D) projects, developing transformation roadmaps and strengthening the skill sets of the workforce.
Singapore’s 5G Rollout
Last month, the Infocomm Media Development Authority (IMDA) announced that Singtel and JVCo (formed by Starhub and M1) has won the 5G Call for Proposal. They will be required to provide coverage for at least half of Singapore by end-2022, scaling up to nationwide coverage by end 2025. While Singtel and JVCo will be allocated radio frequency spectrum to deploy nationwide 5G networks, other mobile operators, including MVNOs, can access these network services through a wholesale arrangement. The networks will also be supplemented by localised mmWave deployments that will provide high capacity 5G hotspots.
In October 2019, IMDA and the National Research Foundation had set aside $40 million to support 5G trials in strategic sectors such as maritime, aviation, smart estates, consumer applications, Industry 4.0 and government applications. Ecosystm Principal Advisor, Jannat Maqbool says, “Reach, performance and robustness of connectivity and devices have long held back the ability to scale with the IoT as well as successful deployment of some solutions altogether. The integration of 5G with IoT has the potential to change that immensely. However, and possibly even more importantly, 5G will see the emergence of a true ‘Internet’, defined as ‘interconnected networks using standardised communication protocols’, made up of ‘things’ enabling never-before contemplated innovation – supporting economic development and community well-being.”
“While 5G offers enormous potential to produce economic and social benefits, to reach that potential we need to evaluate from a strategic perspective what it could mean for industries, employers and communities – then we need to invest in the infrastructure, innovation and associated development required to leverage the technology.”
Singapore’s Industry 4.0 Transformation
The Government is also focused on getting the industry ready for the transformation that 5G will bring. Last week, Singapore announced its first Industry 4.0 trial, where IMDA collaborates with IBM, M1 and Samsung to design, develop, test and benchmark 5G-enabled Industry 4.0 solutions that can be applied across various industries. The trials will begin at IBM’s facility in Singapore and involve open source infrastructure solutions from Red Hat to test Industry 4.0 use cases.
The project will test 5G-enabled use cases for Manufacturing, focusing on areas such as automated visual inspection using image recognition and video analytics, equipment monitoring and predictive maintenance, and the use of AR in increasing productivity and quality. The focus is also on leveraging 5G to reduce the cost of processing, by shifting the load from the edge device to centralised systems.
Ecosystm Principal Advisor, Kaushik Ghatak says, “For some time now, the Singapore Manufacturing industry has been in the quest for higher productivity in order to regain its foothold as a destination of choice for global manufacturing outsourcing. The 5G Industry 4.0 trial is a great initiative to fast-track identification and adoption of the right use cases in Manufacturing, in the areas of automation, visibility, analytics, as well as for opening new revenue streams through servitisation of smart products.”
5G will see increased collaboration in the Tech industry
With the advent of 5G, the market will see more collaboration between government agencies, telecom providers and cloud platform providers and network equipment providers. Governments globally have invested in 5G and so have the network and communications equipment providers. However, telecom providers are unsure of how to monetise 5G and cater to the shift in their customer profile from consumers to enterprises. IBM and Samsung had already announced the launch of a joint platform in late 2019. Collaborations such as these will be key to widespread 5G deployment and uptake.
Talking about the benefits of collaborative efforts such as this, Maqbool says, “Robustness and security built into 5G deployment from the outset is essential to enable the applications and innovation that many are promising the technology will deliver, including the ability to self-scale, automate fault management and support edge processing.”
It is interesting that the solutions developed will be featured at IBM’s Industry 4.0 Studio 5G Solutions Showcase, and that IBM and Samsung will evaluate successful solutions developed during the project for possible use in their operations in a broad range of markets and sectors. “Availability of proven use cases at IBM’s Solutions Showcase centre would benefit local manufactures greatly; in terms of easy access to right skills and proven technology architectures,” says Ghatak. “This initiative is a huge step towards realising the promise of the cyber physical world. The collaboration between the leaders in communications, equipment and software will ensure that the use case development is truly cutting edge.”
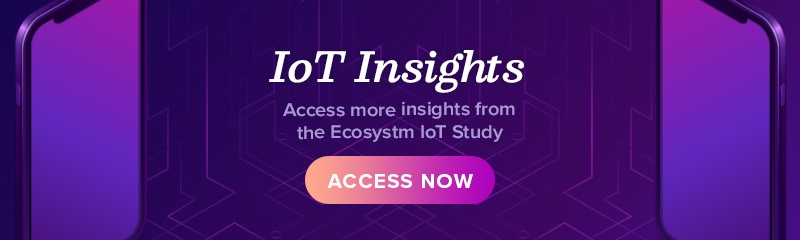
April saw the disruption of normal business operations due to the COVID-19 crisis. However, telecommunications companies continued initiatives to identify the best ways to serve customers and enterprises. The month saw a lot of activity in the 5G space across the globe, including partnerships, innovation in productisation and identifying 5G use cases.
Telecom providers building their 5G capabilities
Ecosystm Principal Advisor, Shamir Amanullah noted in his blog that in the new normal telecom providers have fast evolved as the backbone of business and social interactions. Telecom operators are fervently working towards 5G network and services deployment in order to be an early mover in the market. In China, China Mobile has been one of the leaders in rolling out country-wide 5G. The tender to build around 250,000 fifth-generation wireless network base stations across 28 provincial regions was put out in March and in early April, Huawei emerged as the key winner with the contract to build nearly 60% of the base stations. ZTE also won nearly a third of the contract. Global network equipment providers will find entering the China market as challenge for a number of reasons, including the strength of their local players.
Huawei continues to be under scrutiny in the global market, however British telecom provider chose Ericsson to build the core of its 5G network. BT hopes to create and define a future roadmap of new services such as mobile edge computing, network slicing, enhanced mobile broadband and various enterprise services. The US market is another arena where the battle for 5G will be fought out. The T-Mobile – Sprint merger was finalised in early April. The New T-Mobile is committed to building the world’s best nationwide 5G network, which will bring lightning-fast speeds to urban areas and underserved rural communities alike. Other vendors are also vying for a larger share of the US market. Nex-Tech Wireless, a smaller rural telecom provider based in Kansas, is planning to transition from 4G to 5G by using Ericsson’s Dynamic Spectrum Sharing (DSS) to deploy 5G on existing bands. This will help Next-Tech wireless to leverage existing assets instead of building 5G capabilities from the ground-up – enabling them to seamlessly transfer from 4G to 5G.
The 5G developments are by no means limited mostly to the US and China. Korea’s telecom provider, KT and Far EasTone Taiwan (FET) signed an MOU to collaborate and jointly develop 5G services and digital content. With this deal, KT plans to boost its 5G powered content and services presence through FET.
Tech Vendors evolving their 5G offerings
Network and communications equipment providers have much to gain and more to lose as organisations look to leverage 5G for their IoT use cases. If 5G uptake does not take off, the bigger losers will be the network and communications equipment providers – the real investors in the technology. Also, as telecom providers look to monetise 5G they will find themselves dealing with a completely different customer base – they will take help from tech vendors that have more experience in the enterprise space, as well as industry expertise. Both network equipment vendors and other tech vendors are actively evolving their product offerings. There were numerous examples of this in April.
Microsoft’s decision to acquire Affirmed Networks is an example of how the major cloud providers are trying to be better embedded with 5G capabilities. This month also saw Microsoft announce Azure Edge Zones aimed at reducing latency for both public and private networks. AT&T is a good example of how public carriers will use the Azure Edge Zones. As part of the ongoing partnership with Microsoft, AT&T has already launched a Dallas Edge Zone, with another one planned for Los Angeles, later in the year. Microsoft also intends to offer the Azure Edge Zones, independent of carriers in denser areas. They also launched Azure Private Edge Zones for private enterprise networks suitable for delivering ultra-low latency performance for IoT devices.
The examples go beyond the cloud platform providers. Samsung and Xilinx, have joined forces to enable 5G deployments, with Samsung aiming to use the Xilinx Versal adaptive compute acceleration platform (ACAP) for worldwide 5G commercial deployments. Versal ACAP offers the compute density at low power consumption to perform the real-time, low-latency signal processing needed by 5G. Following the successful pilot of 450 MHz proof of concept 5G network, Nokia has partnered with PGE Systemy, a large energy sector company in Poland to deploy industrial grade 5G solutions and to support energy distribution for its next gen power grid. It is the band of choice for machine-to-machine communications in the energy sector, including smart meters. Nokia also released an AI-as-a-service offering – Nokia AVA 5G cognitive operations – to help telecom providers transform their services with AI-based solutions to support, network, business and operations.
Use cases for 5G adoption firming up
5G promises to revolutionise various industry solutions based on required data rates, low latency, reliability, and machine-type communications. Telecom providers and tech vendors alike are working on developing industry use cases to drive up adoption.
Vodafone Qatar and Dreama Orphan Care Centre and Protection Social Rehabilitation Centre (AMAN) have collaborated to support remote learning and education using 5G technology. This is aimed to enhance virtual education through e-learning, online schools, and connecting teachers and students through high-speed learning environment. In the post-COVID 19 era remote learning is expected to become a key sector and there is immense potential for uptake.
The Manufacturing industry remains a top focus area for 5G providers, with their early adoption of sensors and sensor data analytics. The Smart Internet Lab at the University of Bristol, UK has been awarded a 2 years project by UK’s Department for Digital, Culture, Media and Sport (DCMS) to enable 5G connectivity for the manufacturing sector. The project will primarily work on improving productivity and manufacturing, easy asset tracking and management with involvement of AR/VR technologies and industrial system management.
Gaming is another sector with huge potential for 5G adoption. With cloud gaming, gamers can access a library of popular high-quality games minus the need for expensive hardware which has been the case in the past. China Mobile Hong Kong and Ubitus teamed up to launch a 5G cloud gaming service – UGAME. The application is available for download from the Google Play store. While still at a beta phase, the telecom provider promises a revolutionary gaming experience, where the need for computers or consoles will be lessened by augmented smartphone capabilities.
In the midst of the uncertainties, telecom, network equipment providers and cloud platform providers appear to be gearing up for 5G in enabling a contactless and remote economy.
Identifying and selecting a vendor for your tech project can be a daunting task – especially when it comes to emerging technologies or when implementing a tech solution for the first time. Organisations look for a certain degree of alignment with their tech vendors – in terms of products and pricing, sure, but also in terms of demonstrable areas of expertise and culture. Several factors are involved in the selection process – vendors’ ability to deliver, to match expected quality standards, to offer the best pricing, to follow the terms of the contract and so on. They are also evaluated based on favourable reviews from the tech buyer community.
Often businesses in a particular industry tend to have their unique challenges; for example, the Financial Services industries have their specific set of compliance laws which might need to be built into their CRM systems. Over the years, vendors have built on their industry expertise and have industry teams that can advise organisations on how their business requirements can be met through technology adoption. These experts speak in the language of the industry and understand their business and technology pain points. They are able to customise their product and service offerings to the needs of the industry for a single client – which can then be repeated for other businesses in that industry. Vendors arm themselves with a portfolio of industry use cases, especially when they are entering a new market – and this often gives them an upper hand at the evaluation stage. In the end, organisations want less customisations to keep the complexity and costs down.
Do organisations evaluate vendors on industry experience?
Ecosystm research finds that industry experience can be a significant vendor selection criterion for some tech areas (Figure 1), especially in emerging technologies such as AI. AI and automation applications and algorithms are considered to be distinctive to each industry. While a vendor may have the right certifications and a team of skilled professionals, there is no substitute for experience. With that in mind, a vendor with experience in building machine learning models for the Telecommunications industry might not be perceived as the right fit for a Utilities industry implementation.
Whereas, we find that cybersecurity is at the other end of the spectrum, and organisations perceive that industry expertise is not required as network, applications and data protection requirements are not considered unique to any industry.
Is that necessarily the right approach?
Yes and no. If we look at the history of the ERP solution, as an example, we find that it was initially meant for and deeply entrenched in Manufacturing organisations. In fact, the precursor to modern-day ERP is the Manufacturing Resource Planning (MRP II) software of the 1980s. Now, we primarily look at ERP as a cross-industry solution. Every business has taken lessons on inventory and supply chain management from the Manufacturing industry and has an enterprise-wide system. However, there are industries such as Hospitality and Healthcare that have their niche vendors who bundle in ERP features with their industry-specific solutions. This will be the general pattern that all tech solutions will follow: a) an industry use case will become popular; b) other industries will try to incorporate that solution, and in the process; c) create their own industry-specific customisations. It is important, therefore, for those who are evaluating emerging technologies to cast their net wide to identify use cases from other industries.
AI and automation is one such tech area where organisations should look to leverage cross-industry expertise. They should ask their vendors about their implementations in other allied industries and, in some cases, in industries that are not allied.
For cybersecurity, their approach should be entirely different. As companies move on from network security to more specific areas such as data security and emerging areas such as GRC communication, it will be important to evaluate industry experience. Data protection and compliance laws are often specific to industries – for example, while customer-focused industries are mandated on how to handle customer data, the Banking, Insurance, Healthcare and Public Sector industries have the need to store more sensitive data than other industries. They should look at solutions that have in-built checks and balances in place, incorporating their GRC requirements.
So, the answer to whether organisations should look for industry expertise in their vendors is that they should for more mature tech areas. An eCommerce company should look for industry experience when choosing a web hosting partner, but should look for experience in other industries such as Banking, when they are looking to invest in virtual assistants.
Are some industries more focused on industry experience than others?
Ecosystm research also sought to find out which industries look for industry expertise more than others (Figure 2). Surprisingly, there are no clear differences across industries. The Services, Healthcare and Public Sector industries emphasise marginally more on industry expertise – but the differences are almost negligible.
There are some differences when we look at specific tech areas, however. For example, industries that may be considered early adopters of IoT – Transportation, Manufacturing and Healthcare – tend to give more credit to industry experience because there are previous use cases that they can leverage. There are industries that are still formulating standards when it comes to IoT and they will be more open to evaluating vendors that have a successful solution for their requirement – irrespective of the industry.
The Healthcare Industry Example
Ecosystm Principal Analyst, Sash Mukherjee says, “In today’s fast-evolving technology market, it is important to go beyond use cases in only your industries and look for vendors that have a demonstrated history of innovation and experience in delivering measurable results, irrespective of the industry.” Mukherjee takes the example of the Healthcare industry. “No one vendor can provide the entire gamut of functionalities required for patient lifecycle management. In spite of recent trends of multi-capability vendors, hospitals need multiple vendors for the hospital information systems (HIS), ERP, HR systems, document management systems, auxiliary department systems and so on. For some areas such as electronic health records (EHR) systems, obviously industry expertise is paramount. However, if healthcare organisations continue to look for industry expertise and partner with the same vendors, they miss out on important learnings from other industries.”
Talking about industries that have influenced and will influence the Healthcare industry in the very near future, Mukherjee says, “Healthcare providers have learnt a lot from the Manufacturing industry – and several organisations have evaluated and implemented Lean Healthcare and Six Sigma to improve clinical outcomes. The industry has also learnt from the Retail and Hospitality industries on how to be customer focused. In the Top 5 Healthtech trends for 2020, I had pointed out the similarities between the Financial and Healthcare industries (stringent regulations, process-based legacy systems and so on). As the Healthcare industry focuses on value-based outcomes, governments introduce more regulations around accountability and transparency, and people expect the experience that they get out of their retail interactions, Healthtech start-ups will become as mainstream as Fintech start-ups.”
It is time for tech buyers to re-evaluate whether they are restricting themselves by looking at industry use cases, especially for emerging technologies. While less industry customisations mean easier deployments, it may also hamper innovation.