Last week I wrote about the need to remove hype from reality when it comes to AI. But what will ensure that your AI projects succeed?
It is quite obvious that success is determined by human aspects rather than technological factors. We have identified four key organisational actions that enable successful AI implementation at scale (Figure 1).
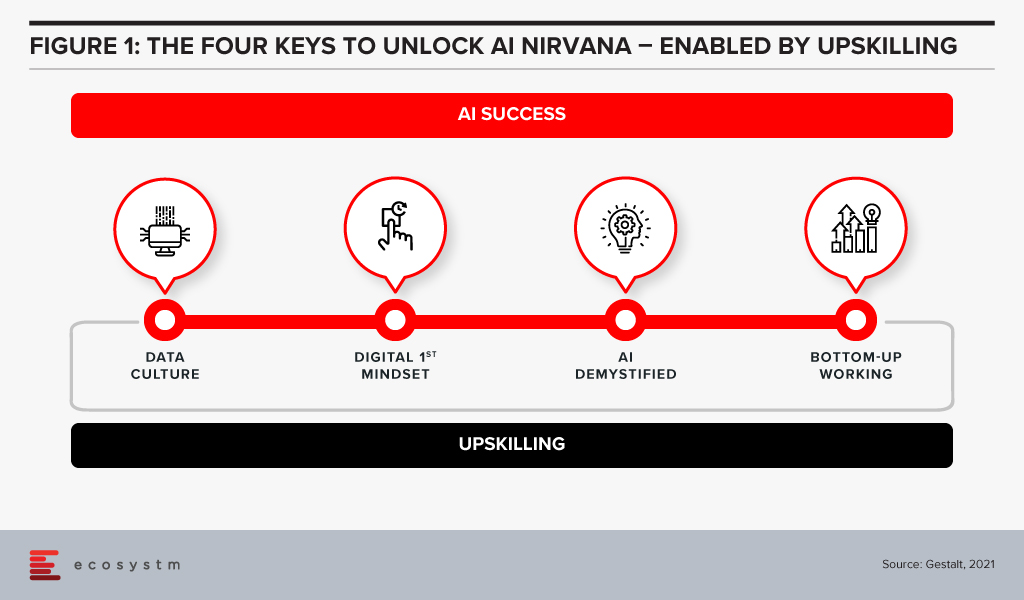
#1 Establish a Data Culture
The traditional focus for companies has been on ensuring access to good, clean data sets and the proper use of that data. Ecosystm research shows that only 28% of organisations focused on customer service, also focus on creating a data-driven organisational culture. But our experience has shown that culture is more critical than having the data. Does the organisation have a culture of using data to drive decisions? Does every level of the organisation understand and use data insights to do their day-to-day jobs? Is decision-making data-driven and decentralised, needing to be escalated only when there is ambiguity or need for strategic clarity? Do business teams push for new data sources when they are not able to get the insights they need?
Without this kind of culture, it may be possible to implement individual pieces of automation in a specific area or process, applying brute force to see it through. In order to transform the business and truly extract the power of AI, we advise organisations to build a culture of data-driven decision-making first. That organisational mindset, will make you capable implementing AI at scale. Focusing on changing the organisational culture will deliver greater returns than trying to implement piecemeal AI projects – even in the short to mid-term.
#2 Ingrain a Digital-First Mindset
Assuming a firm has passed the data culture hurdle, it needs to consider whether it has adopted a digital-first mindset. AI is one of many technologies that impact businesses, along with AR/VR, IoT, 5G, cloud and Blockchain to name a few. Today’s environment requires firms to be capable of utilising a variety of these technologies – often together – and possessing a workforce capable of using these digital tools.
A workforce with the digital-first mindset looks for a digital solution to problems wherever appropriate. They have a good understanding of digital technologies relevant to their space and understand key digital methodologies – such as Customer 360 to deliver a truly superior customer experience or Agile methodologies to successfully manage AI at scale.
AI needs business managers at the operational levels to work with IT or AI tech teams to pinpoint processes that are right for AI. They need to make an estimation based on historical data of what specific problems require an AI solution. This is enabled by the digital-first mindset.
#3 Demystify AI
The next step is to get business leaders, functional leaders, and business operational teams – not just those who work with AI – to acquire a basic understanding of AI.
They do not need to learn the intricacies of programming or how to create neural networks or anything nearly as technical in nature. However, all levels from the leadership down should have a solid understanding of what AI can do, the basics of how it works, how the process of training data results in improved outcomes and so on. They need to understand the continuous learning nature of AI solutions, getting better over time. While AI tools may recommend an answer, human insight is often needed to make a correct decision off this recommendation.

#4 Drive Implementation Bottom-Up
AI projects need alignment, objectives, strategy – and leadership and executive buy-in. But a very important aspect of an AI-driven organisation that is able to build scalable AI, is letting projects run bottom up.
As an example, a reputed Life Sciences company embarked on a multi-year AI project to improve productivity. They wanted to use NLP, Discovery, Cognitive Assist and ML to augment clinical proficiency of doctors and expected significant benefits in drug discovery and clinical trials by leveraging the immense dataset that was built over the last 20 years.
The company ran this like any other transformation project, with a central program management team taking the lead with the help of an AI Centre of Competency. These two teams developed a compelling business case, and identified initial pilots aligned with the long-term objectives of the program. However, after 18 months, they had very few tangible outcomes. Everyone including doctors, research scientists, technicians, and administrators, who participated in the program had their own interpretation of what AI was not able to do.
Discussion revealed that the doctors and researchers felt that they were training AI to replace themselves. Seeing a tool trying to mimic the same access and understanding of numerous documents baffled them at best. They were not ready to work with AI programs step-by-step to help AI tools learn and discover new insights.
At this point, we suggested approaching the project bottom-up – wherein the participating teams would decide specific projects to take up. This developed a culture where teams collaborated as well as competed with each other, to find new ways to use AI. Employees were shown a roadmap of how their jobs would be enhanced by offloading routine decisions to AI. They were shown that AI tools augment the employees’ cognitive capabilities and made them more effective.
The team working on critical trials found these tools extremely useful and were able to collaborate with other organisations specialising in similar trials. They created the metadata and used ML algorithms to discover new insights. Working bottom-up led to a very successful AI deployment.
We have seen time and again that while leadership may set the strategy and objectives, it is best to let the teams work bottom-up to come up with the projects to implement.
#5 Invest in Upskilling
The four “keys” are important to build an AI-powered, future-proof enterprise. They are all human related – and when they come together to work as a winning formula is when organisations invest in upskilling. Upskilling is the common glue and each factor requires specific kinds of upskilling (Figure 2).
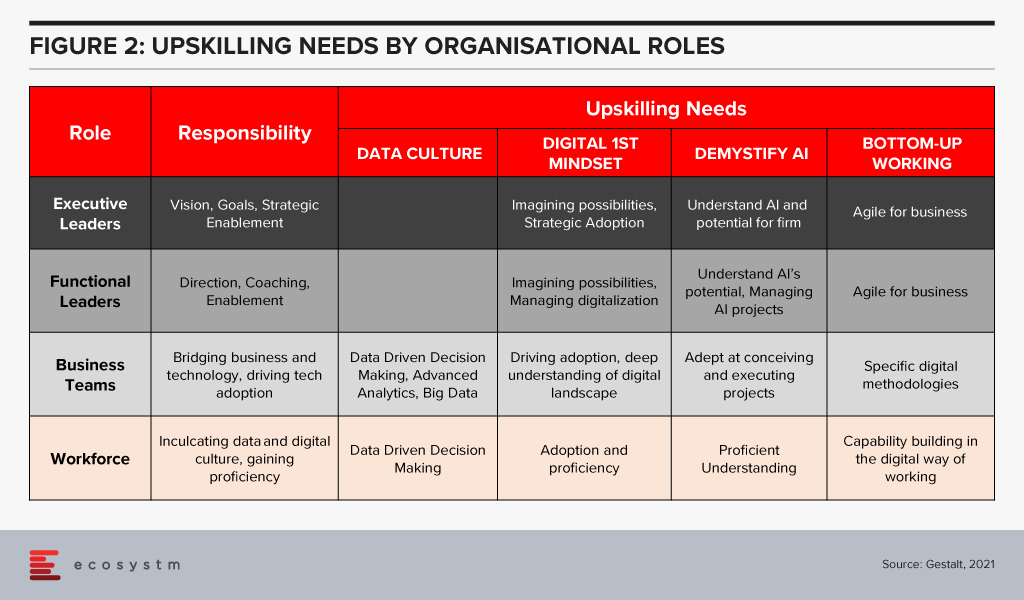
Upskilling needs vary by organisational level and the key being addressed. The bottom line is that upskilling is a universal requirement for driving AI at scale, successfully. And many organisations are realising it fast – Bosch and DBS Bank are some of the notable examples.
How much is your organisation invested in upskilling for AI implementation at scale? Share your stories in the comment box below.
Written with contributions from Ravi Pattamatta and Ratnesh Prasad
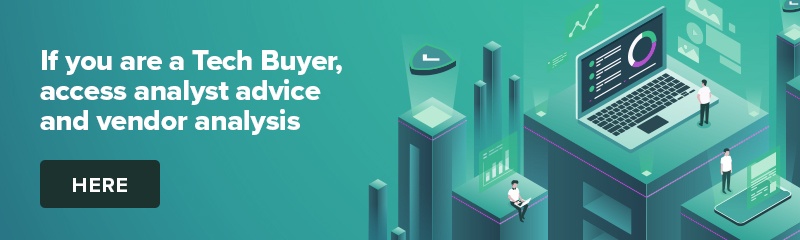
Kaushik Ghatak (Principal Advisor, Digital Transformation and Supply Chain) and Liam Gunson (Director, Product and Solutions)
Authored by attending Ecosystm analysts, Ullrich Loeffler (Chief Operating Officer),Bosch Software Innovation (Bosch SI) hosted its annual analyst briefing in Singapore on 6th December 2019 to provide an update on its business, strategy and solution portfolio in the APAC region.
Bosch has expanded its capability and reshaped its go-to-market approach in a bid to not only position itself as a world leading IoT company, but also help move the IoT market forward.
A number of new solutions were demonstrated through the day. From tenants asking their building management if the gym was busy, to smartphones detecting a manufacturing fingerprint so you could avoid buying a counterfeit.
At the heart of the business updates though was a new organisational approach to prove markets and integrate user perspectives into solution development. Bosch is looking to achieve this by setting up dedicated, cross-divisional entities which can focus on user needs to drive growth while collating requirements for the Bosch SI centres.
Bosch SI essentially will perform a role of an IoT business incubator within Bosch Group, and once a vertical within Bosch SI has reached a certain level of business, it is spun off into a separate company focusing on that area. There are three business units that have met the threshold and have spun off so far.
Broader challenges still remain for IoT adoption. Patchy connectivity, varied regulation, and a lack of standardisation will continue to hamper the IoT market. However, from a user perspective the timing is right. Ecosystm research shows that while IoT uptake is limited, intention is strong. Enterprises will be looking for partners with a willingness to understand their needs and design around them, in order to help get initial projects off the ground.
Bosch Business Update – From Innovation to Commercialisation
Bosch SI was created to build Internet of Things (IoT) solutions, leveraging Bosch’s 133-year experience in developing and manufacturing products for the automotive, industrial and consumer segments. Founded in 2008, by 2019 Bosch SI has established 10 global offices, of which some have solution development capabilities, employing over 700 IoT experts. Four of the Bosch SI offices are located in Asia Pacific – Singapore, Nanjing, Shanghai and Tokyo.
Figure 1: Bosch Software Innovations in Numbers
The Bosch IoT Vision and Strategy is not limited to Bosch SI’s but spans across the full Bosch Group. An indication of the dedication to the IoT story is that Bosch is committed to enabling connectivity for all existing product portfolios ranging across its industrial, automotive, manufacturing and consumer product lines by 2021.
Another indication of Bosch’s IoT business maturing is that in 2018 Bosch it formed 3 new subsidiaries, each being a dedicated entity to take targeted IoT Industry solutions to market. The new business entities focus on
- Connected Industry
- Connected Mobility
- Residential IoT
with other areas such as Agriculture, Retail, Energy, Mobility, Manufacturing and Home & Building as potential future spin-offs. The announcement is significant as it separates the innovation and commercialisation functions. Bosch SI becomes the dedicated R&D and incubation engine to take new industry solutions to a defined threshold before a dedicated entity is formed to achieve commercial scale.
Despite the fact that IoT has been greatly overhyped since the term was coined by Kevin Ashton in 1999, Ecosystm research shows evidence that adoption is accelerating across the region. Figure 2 outlines the current and planned adoption of ‘sensor-based analytics’ within organisations. The research strongly supports Bosch’s timing for investments in scaling the commercialisation of its solutions.
Figure 2: Industry Adoption of Sensor-Based Analytics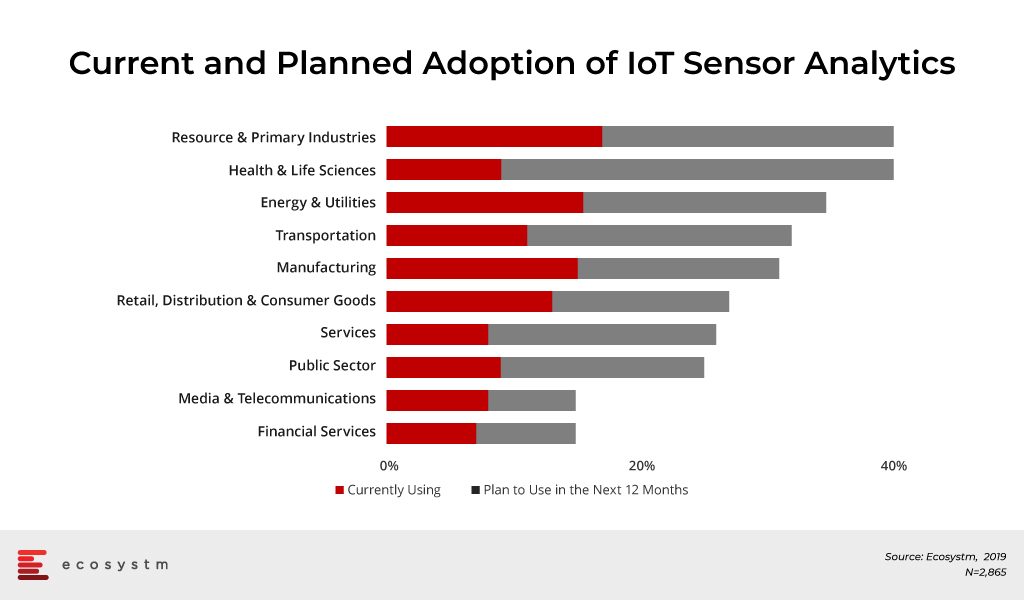
Market Pull over Technology Push is creating proven Industry Use Cases
The locations and specialisations of Bosch’s Innovation Centres across Asia are no accident and result directly from engagements with local clients. Each innovation centre specialises in certain solutions that have arisen from the productisation of solutions developed for customers. This ‘market pull’ strategy is a clear differentiation to the commonly practiced ‘technology push’ approach which has seen many vendors struggle to gain traction for their IoT solutions. Key industry solutions developed by Bosch SI are:
- Agriculture – Bosch Plantect: (Japan). Plantect is a sensor-based monitoring system for early detection and prevention of plant diseases in greenhouses. The current solution targets greenhouse farmers for tomatoes, cucumber and strawberries.
- Smart Building – Bosch Lift Manager (Singapore). Lift Manager is an AI-supported solution that can be retrofitted in existing lifts with set algorithms to monitor and predict lift malfunctions and enable predictive maintenance.
- Smart Building – Connected Buildings (Singapore). Bosch Connected Building leverages cameras and sensors to optimise business operations such as Air Quality, Light Monitoring & Control, Lift Monitoring, Occupancy Tracking, Asset Tracking, Carpark Monitoring, and Object Tracking.
- Manufacturing – Secure Product Fingerprint Solutions (China). Secure Product Fingerprint captures a unique fingerprint for products to combat counterfeits and connect manufacturers with their users.
The Bosch IoT Ecosystem – Open Source and API enabled Platform
Bosch has realised that IoT is a concept that cannot be owned and delivered by a single entity. As such Bosch aims to establish its Bosch IoT Suite as the platform to connect any Bosch or third party “things” to deliver targeted industry services and solutions.
Bosch IoT Suite can be deployed on Bosch’s own IoT Cloud or through Cloud partners such as AWS, Microsoft or Huawei (for China only). It is a PaaS offering that packages unified device APIs to connect things with device management, software updates over the air, data management and security capabilities. An inbuilt analytics engine assists with business logic tools to drive business value out of the data collected. The open source and open standards architecture promote the development of in-house or third-party industry applications as platform add-ons and use cases.
Bosch and Market Outlook
IoT has been one of the most hyped ‘buzz words’ for the last few years but true market adoption is yet to follow suit. Ecosystm research shows that market intention is positive with more industry-focused uses cases and simpler ‘plug and play’ style solutions available that require less CapEx and shorter time to value.
Bosch is well positioned to capitalise on this trend. Its focus on developing proven use cases for targeted industry sectors and then working with anchor customers and testing the solutions internally within Bosch, is a clear differentiator in the market. Commercially scaling these solutions will remain the key challenge as decision stakeholders may not be the key beneficiary of the solution. In the connected building example, tenants will be the key beneficiary of finding quiet gym slots or having better air quality but it remains questionable whether this will convince the building owner or operator to put pen to paper and sign-off on relevant IoT investments. An area that Bosch needs to focus on, is the articulation of its business proposition and more importantly connect this to the business value to prospects and customers. As solutions scale in the market, broader sales and partner teams will need to be enabled to bring this message to the relevant stakeholders. The fact that these stakeholders may sit outside Bosch’s traditional comfort zone will not make this endeavor easier.
Bosch will also face varying market regulations that could create road bumps in scaling its solutions. The Bosch Lift Manager solution as an example provides sensor diagnostics for predictive maintenance scheduling. Many existing lift maintenance contracts however follow local regulations that require ongoing scheduled servicing of elevators which reduces the cost savings potential.
The decision to establish standalone IoT entities is seen as a strong commitment and the right move to take advantage of the presented IoT opportunity. The high degree of customer advocacy and industry experience further makes Bosch a strong contender of the Industry 4.0 revolution.